What Is Electron Beam Drilling? Process, Benefits & Uses
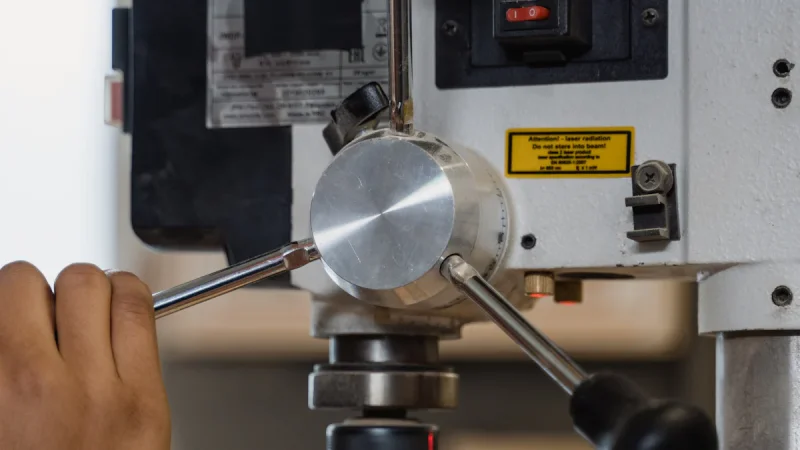
Electron beam drilling establishes itself in advanced precision engineering as an efficient non-traditional machining procedure providing precise output. The focused beam of high-velocity electrons enables this method to create holes of sizes ranging from microscopic to millimetric diameters inside rigid materials. The technique finds its best applications in aerospace, automotive, and microelectronics sectors because precise drilling alongside minimal heat effects is vital.
Both the procedure of electron beam drilling and its advantages and practical industrial applications will be explained in this guide. This complete article satisfies every inquiry for students, engineers, and those seeking information about this topic.
EBD is a thermal machining technique that utilizes high-speed electrons that focus on material surfaces to erase material through heat-based melting and vaporization. The vacuum-generated electron beam produces holes with diameters reaching down to several micrometers.
Electron Beam Drilling belongs to non-contact machining processes and achieves exceptional outcomes when cutting challenging metal components with complex drilling characteristics.
Ti potrebbe interessare:
Electron beam drilling performs its operations through a methodical sequence that mainly runs inside vacuum chambers:
Tungsten filament production heats up to generate electrons by achieving thermionic emission. The electric field pushes electrons to move with high velocities.
High-speed electrons subsequently pass through electromagnetic lenses to produce a small energetic beam.
Direct beam energy transmission into thermal energy at the workpiece starts the material melting and vaporization process. The pressure builds due to molten material, which pushes it out through the hole opening in a clean form.
The operation occurs inside an enclosed vacuum that blocks electron scattering from air particles, thus delivering precise beam performance with concentrated energy output.
The practice of electron beam drilling delivers multiple substantial advantages over ordinary drilling operations. Here are the key benefits:
Through this technique, it is possible to create holes that preserve exact dimensions and maintain high ratios of length to width, no matter the size or fragility of the component.
Following its narrow beam concentration, the material surrounding the target stays free from heat-induced damage.
The drilling capability of these three materials and superalloys specifically meets aerospace and defense operation requirements.
The absence of mechanical contact during this process stops tools from wearing down, thus eliminating the need for regular replacements.
EDM produces holes with no visible burrs, which eliminates the requirement for subsequent post-processing steps.
The high effectiveness of EBD comes with certain drawbacks.
- Vacuum Requirement: Equipment prices rise substantially when vacuum conditions become necessary.
- High Initial Cost: Due to its initially expensive equipment demands, EBD functions only in industries operating with large budgets.
- Not Suitable for All Materials: The procedure fails to work effectively when drilling through non-conductive materials or strongly reflecting light.
Technologies from multiple high-tech fields implement electron beam drilling because this method provides outstanding reliability and unparalleled precision.
Jet engines and turbine blades develop cooling holes as a result of the procedure.
This technology produces precision transmission components while helping to build fuel injector nozzles.
It perfectly serves the industry in making micro-holes in printed circuit boards (PCBs) and microelectromechanical systems (MEMS).
Medical tools and implants need exact and sterile drilling functions, so electron beams serve this purpose.
Even though they are both non-contact thermal procedures, they differ significantly in the following ways:
Feature | Electron Beam Drilling | Laser Drilling |
Precision | Higher | Lower |
Hole Size | Smaller and more accurate | Larger and less precise |
Material Suitability | Excellent for hard metals | Better for soft to medium-hard materials |
Heat Affected Zone | Very low | Moderate |
Cost | Higher | Lower |
The industry’s growing need for small and intricate components will elevate the importance of electron beam drilling methods. Scientists work to decrease technology costs to make this solution available across multiple industrial segments. EBD machines attract new potential through AI integration and automation, transforming them into faster, more innovative, and versatile platforms.
Electron Beam Drilling is a high-precision, non-contact machining technique specialized for making fine holes in hard materials through precise hole-making with low distortion levels. The extensive requirements for vacuum conditions and substantial startup costs do not hinder the adoption of this method since it provides exceptional results to industries requiring precision and reliability.
This manufacturing industry of the future relies on EBD because the technology produces designs that standard tools previously could not create. The technology will sustain its crucial position in advancing engineering breakthroughs through its development process.
Q1. What are the possible dimensions of holes that EBD drilling methods can create?
A: The precision holes created by the electron beam drilling process range in size from micrometers to millimeters.
Q2. Which essential element does the vacuum play in electron beam drilling operations?
A: Atomic particle beams concentrate their energy path toward the workpiece because a vacuum prevents electron scattering.
Q3. Does electron beam drilling work effectively with all types of metals as an option?
A: Excellent performance in titanium, nickel alloys, and tungsten is achieved using electron beam drilling. Nevertheless, it performs less well when non-conductive materials are used.
Q4. What sets electron beam drilling apart from regular drilling practices?
A: The electrical method of EBD operates through an electron beam instead of mechanical mechanisms to deliver precision and tool wear immunity.
Q5. Which industries find the best success through electron beam drilling?
A: Industries like aerospace, automotive, medical, and electronics benefit significantly due to the need for micro-precision and high-quality finishes.
Ti potrebbe interessare:
Segui guruhitech su:
- Google News: bit.ly/gurugooglenews
- Telegram: t.me/guruhitech
- X (Twitter): x.com/guruhitech1
- Bluesky: bsky.app/profile/guruhitech.bsky.social
- GETTR: gettr.com/user/guruhitech
- Rumble: rumble.com/user/guruhitech
- VKontakte: vk.com/guruhitech
- MeWe: mewe.com/i/guruhitech
- Skype: live:.cid.d4cf3836b772da8a
- WhatsApp: bit.ly/whatsappguruhitech
Esprimi il tuo parere!
Che ne pensi di questa notizia? Lascia un commento nell’apposita sezione che trovi più in basso e se ti va, iscriviti alla newsletter.
Per qualsiasi domanda, informazione o assistenza nel mondo della tecnologia, puoi inviare una email all’indirizzo guruhitech@yahoo.com.
Scopri di più da GuruHiTech
Abbonati per ricevere gli ultimi articoli inviati alla tua e-mail.